主讲老师: 宋曦(培训费:1.5-2万元/天)
工作背景:
23年生产管理经验、其中16年制造业生产全面管理工作实践经验7年制造业班组建设、生产计划、精益改善咨询实战经验日产训五项全能(TWI+MTP6单元)认证老师(国内排名前50名)管理沙盘教学认证讲师(擅长:班组...
主讲课程:
班组长系列课程:《一线班组长五项实用管理技能提升训练》(权版课程)《“华为”式班组长综合管理技能提升训练》(权版课程)《金牌班组长六项现场管理技能提升》TWI-JI/JM/JR/JS ...
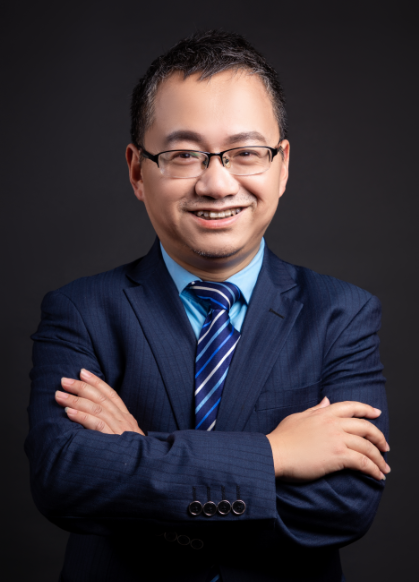
生产现场6S系统落地与实施课程大纲详细内容
课程分类: 6S(5S)
课程目标:
保证学员系统学习目前国内最先进6S管理理论、掌握6个S实施要点;
保证学员系统掌握企业有效、持续开展6S而不会半途而废的秘籍;
保证学员系统学习掌握生产现场目视化、标准化、规范化建立方法;
保证学员及时掌握减少浪费,降低管理难度,提高管理能力、反应能力、改善能力;
保证学员在车间现场使企业文化和经营理念落地,保持一致性,提升企业形象。
课程对象:部门经理、现场改善项目负责人、车间、仓库管理人员、办公室6S专员
课程时间:1天,6小时/天
视频案例&破冰讨论:办公室找文件
第一讲:6S基础知识介绍
一、6S发展历史
1.美国波音公司与二战5S故事
2.日本5S发展故事
二、6S与其它知识逻辑关系
1.6S与精益生产逻辑关系
2.6S与PMC、TQC关系
三、6S实施的目的与好处
1.目的:改变人、改变人员作业习惯;
2.好处:减少浪费、提升效率、改善品质、降本增效
四、6S目前企业实施过程问题与原因
1.问题:
1)做得好的很少;
2)能坚持的不多。
2.原因:
1)领导很少参与
2)少数人在行动
3)配套工具不足
4)不能执之以恒
5)根源无法解决
6)没有奖罚措施
视频案例&互动思考:日本军官参观中国北洋水师兵舰
第二讲:6S导入前准备工作
一、思想准备
宣传、会议、仪式一样不能少!
二、学习准备
反反复复、持续不断、全员式的培训!
三、组织准备
专门的领导小组、甚至是专人负责!
四、制度准备
建立一套检查、监督改善、问题跟踪、奖罚制度!
第三讲:6S步骤详解
一、整理
1.主要理解
2.具体做法:
1)减少现场物品数量
2)区分要与不要标准
3)找到水笼头关掉
3.推行要领:
1)要和不要的标准制定:
a什么物品可以留在现场、什么物品不能
b现场物品留多少?
2)要和不要的制度制定:
a当日生产不需要的材料——不要出现
b当日生产完成的产成品——快速流转
c当日生产遗留多余材料——立返仓库
d本周不用的工装夹具品——返回仓库
4.注意事项:以往整理实施过程中的教训
1)水笼头不关——天天拖地!
2)生产计划失控——现场地制品太多!
3)物料领用制度混乱——现场东西太多!
4)品质管理不完善——现场返工不及时!
视频案例&互动思考:如何提升上飞机效率
二、整顿
1.主要理解
2.具体做法:
1)做好下面的三定工作
2)做好三定后定标准贴在需要三定的地点(目视化)
3)目视化(划区、划线、物品或区域标识)
4)根据实际情况增加必要的装备
3.推行要领:三定
1)定点(定位)
2)定容(面积)
3)定量(数量)
4.注意事项:
1)做好规划
2)制定标准
3)先期试点
4)培训到位
5)方便快捷
6)现场观察
视频案例分析1&互动思考:小张的办公桌
三、清扫
1.主要理解
2.具体做法:
1)划分好责任区
2)制定清扫标准
3)上下全员参与
4)建立检查制度
3.推行要领:
1)观念正确
2)培训到位
3)领导检查
4)问题改善
4.全员参与与设备保养(TPM)操作手法
1)先设定清扫制度养成设备清扫习惯
2)设定设备点检表进行定期有效点检
3)在清扫与点检中发现设备存在问题
4)对发现设备问题加以分析解决改进
5.注意事项:
1)标准要有
2)持之以恒
3)及时改善
4)责任到位
案例分析&互动思考:台州一家电机企业清扫过程中的问题解决
四、清洁
1.主要理解
2.具体做法:
1)巩固前面3个S
2)形成标准化、制度化
3.推行要领:
1)找出所有现场存在问题的水笼头
2)对水笼头加以解决
3)对问题根源加以分析解决
4)形成制度化加以维持
4.注意事项:
1)根源问题未解决
2)制度落实不到位
3)管理系统未调整
4)慢慢流于形式化
五、素养
1.主要理解
2.具体做法:
1)培训与宣导
2)仪表细节要求
3.推行要领:
1)早会培训与宣传
2)不断地检查纠正
3)随时随地教育
4)从小事抓起。
4.注意事项:
1)管理者以身作则
2)现场管理多引导
3)注重团队氛围打造
4)引导而不是惩罚
案例分析&互动思考:浙江某鞋企通过4S工作开展实现员工素养的提升
六、安全
1.主要理解
2.具体做法:
1)培训与宣导
2)注意预防工作
3.推行要领:
1)前3S做到位
2)提升员工意识
3)日常检查到位
4.注意事项:
1)员工没有做必要培训
2)现场管理未能时时检查
3)日常检查流于形式
七、6S知识汇总
1.6S关键词提练
1)整理:要与不要;
2)整顿:三定(定点、定容、定量)
3)清扫:清扫即点检
4)清洁:巩固与清除水龙头
5)素养:培养好习惯
6)安全:预防与检查
2.6S与浪费改善关系
1)整理:改善对象——空间/质量目的——让员工看到浪费、提升利润
2)整顿:改善对象——时间/效率目的——让员工形成消除浪费之理念
3)清扫:改善对象——设备/环境目的——让员工现场发现浪费现象
4)清洁:改善对象——可视/标准目的——让员工动手消除浪费及根源
5)素养:改善对象——行为/规则目的——让员工养成良好的工作习惯
第四讲:目视化与标准化
一、目视化
1.正确理解:
1)只有看到才能管到
2)问题自然发现
2.四大要求
1)一目了然
2)提升效率
3)减少失误
4)信息畅通
3.目视化的六大分类
4.目视化实施过程中具体做法
1)必须保证任何场合一目了然(标识、划分、操作指导贴出来)
2)所以上述工作必须由公司统一标准制作
3)对所在车间、仓库人员进行培训教育,培养习惯
4)不断在定期6S检查中发现还未做到位的地方
5)不断自我检讨存在的问题加以改进
案例分析&互动思考:某制造企业目视化管理样板
二、标准化
1.标准基本理解
2.标准化四大效果
1)使现场管理客观化
2)使现场问题显性化
3)使管理工作简单化
4)使管理效率最大化
3.标准化五大内容
4.标准化三大步骤
5.标准化实施过程中具体做法
案例分析&互动思考:某国内某企业的《空气压缩机操作规程》的问题分析
第五讲:6S企业导入实施步骤
一、回顾第二大点
1.宣传
2.培训
3.组织
4.制度
二、策划工作
1.定阶段
2.定目标
3.定时间
三、检查体系
1.建立检查制度
2.领导一定要参与
3.结果评比公布
四、改善体系
1.检查问题一定要跟踪
2.找到水龙头
3.制度上调整与完善
五、奖罚体系
1.及时兑现的奖罚体系
2.与工资挂钩的绩效体系
学员分组总结与分享