主讲老师: 郭涛(培训费:2-2.5万元/天)
工作背景:
15年德资,日企,台资与民企生产与供应链管理经验1000多家生产型企业诊断与评估经历采购与供应链管理培训认证高级讲师,国家中级经济师北大,上海交大,浙大,华东理工等高等院校合作讲师
主讲课程:
采购与供应链管理系列《价值实现-专业采购成长之路4.0》10天版、《采购策略制定与策略实施》、《供应商战略寻源,筛选,评估,选择与绩效管理》、《采购计划,质量,交期与绩效管理》、《采购全成...
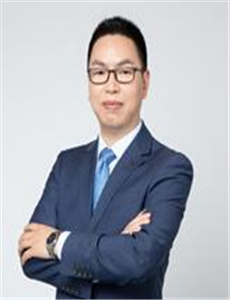
精益现场持续改善课程大纲详细内容
课程分类: 现场管理精益生产
课程目标:
1、了解持续改善的五大核心价值观
2、明确现场管理者进行持续改善的五大关键理念
3、掌握发现改善时机的五种工具,明确需要改善的三大问题
4、掌握从六大方面分析现有方法问题的思路
5、掌握创新的三种类型,影响创新的五种障碍与产生创意的三种有效方法
6、掌握制定对策的六大理念与制定对策需要考虑的三方面内容
7、掌握实施计划的三大核心理念与实施跟进的两种方法
8、掌握效果评估的三大对象与评估的两大阶段
9、掌握持续改善有效推行的六大要领与六大关键点
课程对象:精益/生产经理、持续改善经理、物流经理、车间主任,一线主管等
课程时间:2天/12H(每天6H)
第一讲:持续改善背景与概论
一、为什么要进行持续改善
视频案例导入:丰田公司案例
二、持续改善的五大核心价值观
二、持续改善戒律
三、现场管理者技能培训工作与具体方法
四、丰田持续改善发展历程
五、持续改善关键理念
六、持续改善的基本模式:持续改善六步法
视频案例分析:物料架改善案例
第二讲:发现改善机会
一、改善与解决问题
1、 改善与问题定义
2、 问题的三种类型与层次
3、 不同问题层次实施对应工具
案例分析:中国护士与美国护士配错药
二、持续改善的态度
1、从源头获取事实
2、不要被先入之见所动摇
3、进行全面的观察—5WHY思维
案例分享:5WHY分析表
4、冷静的态度—理性大于情感
三、持续改善的分析技术
案例分享:生产数量损失表
四、机会(问题)意识提升
案例分析:小孩为谁而玩
五、发现浪费和确认改善机会的基本方法
1、将业绩同标准进行比较
2、生产分析板
3、VSM图/七种浪费/5S
角色扮演模拟:投入与产出游戏演练
第三讲:分析现有方法
一、工作分析
1、 工作分析单元
2、 一线主管技能培训(TWI)工作方法分析
3、 丰田工作分析
案例分享:某500强企业工作分析表
现场演练:工作分析(可用企业案例)
二、动作分析
1、动作分析—动素
案例分析:铅笔移动分析
现场演练:动作分析(可用企业案例)
三、时间研究
1、时间观测要点
案例分享:写字时间研究
现场演练:时间研究(可用企业案例)
四、标准化工作
1、标准化工作的三要素
2、标准化工作表设计与实施
案例分析:螺丝加工
案例演练:标准化工作表(可用企业案例)
四、设备损耗分析
1、设备停机
2、设备换模
3、设备周期时间
4、小的停机
5、不良品和返工
6、开机损耗或产量损耗
五、价值流分析
案例分析:客户的特殊订单处理流程
案例分析:A产品价值流程图
现场演练:产品加工流程图(可用企业案例)
第四讲:产生新的创意
一、影响创意的常见障碍
视频案例分析:幸福来敲门片段
二、针对创造性和团队的创意技巧
现场演练:连线
三、产生创意的具体方法
1、 奥斯本的检查表
2、 动作经济原则
3、 5W1H与ECRS
4、 头脑风暴法
现场演练:如何运用头脑风暴法
第五讲:制定实施计划
一、制定计划需要考虑的六大要素
视频案例分析:三国演义片段
二、持续改善计划作成
案例分享:持续改善计划
现场演练:制作改善计划
第六讲:实施计划与结果评估
一、实施计划的三大关键理念
视频案例分析:历史转折中的邓小平片段
二、贯彻实施对策
1、对策实施之有效检查
2、对策实施之遵守率与改善
三、评价结果与过程
1、过程评价
2、结果评价
3、因果链验证
案例分享:某企业改善评估表
总结,答疑!